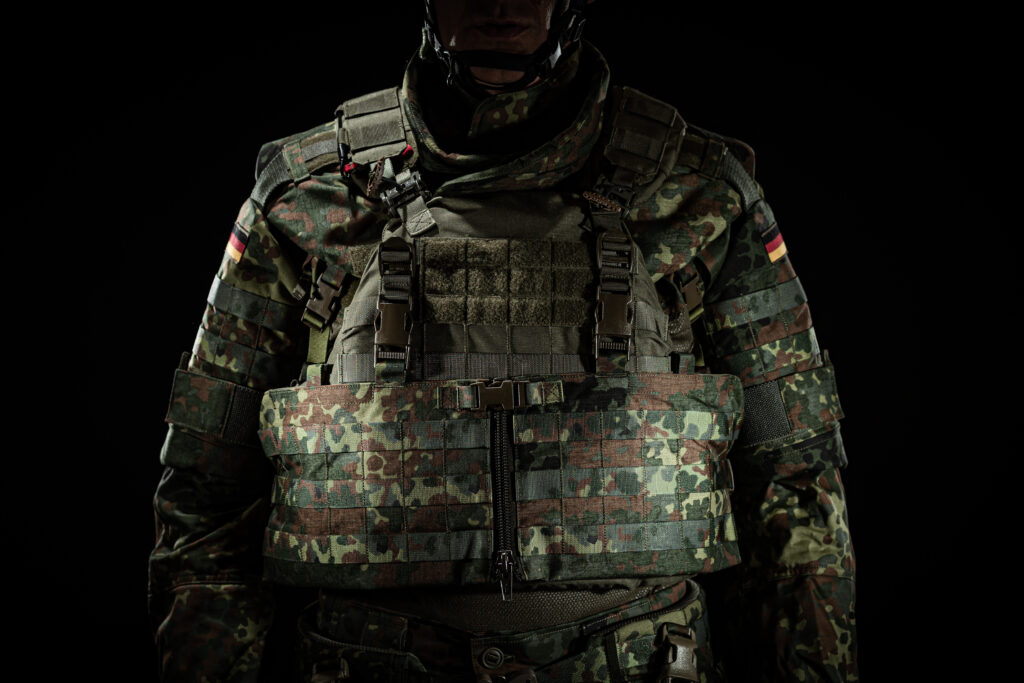
Aramide ou polyéthylène pour les gilets pare-balles
De nos jours, il est difficile d’imaginer les policiers et les militaires sans gilet pare-balles.
Les gilets pare-balles ont été produits pour la première fois au début du 20e siècle. Ils étaient alors fabriqués en fibres de soie. La soie était chère et, en raison de son coût, le matériau a été jugé inadapté à la fabrication de gilets de protection en série.
Avec le temps, une alternative viable a été trouvée sous la forme d’un tissu en fibres aramides. Aujourd’hui, l’aramide a cédé la place au para-aramide et au polyéthylène.
Le para-aramide et le polyéthylène sont des fibres synthétiques extrêmement résistantes, mais leur composition chimique est fondamentalement différente (elles sont également visiblement différentes, à en juger par leur seule couleur : le para-aramide est jaune, tandis que le polyéthylène est blanc).
Dans cet article de blog :
- Qu’est-ce que le para-aramide ?
- Caractéristiques du para-aramide
- Qu’est-ce que le polyethylene haute performance ?
- Caractéristiques du polyéthylène haute performance
- Difference entre le para-aramide et le polyethylene haute performanc
- Résistance et durabilité
- Performance multicoups
- Potentiel de performance du polyéthylène haute performance
- Matériaux utilisés pour la production de balistiques légère
- Matériaux utilisés pour la production de balistiques renforcées
- Résumé
Qu’est-ce que le para-aramide ?
Le para-aramide est un matériau organique produit industriellement à partir de polyamides aromatiques (polyaramides). Il a été mis au point au milieu des années 1960 par l’entreprise chimique américaine DuPont.
Aujourd’hui, la fibre para-aramide est fabriquée sous différentes marques, notamment :
- Kevlar®
- Twaron®
- Taparan®
- Technora®
Caractéristiques du para-aramide
Les fibres para-aramides présentent une résistance élevée à la traction à faible étirement. Il en résulte d’excellentes caractéristiques de protection balistique contre un large éventail de types de balles. Il en résulte également une remarquable capacité de survie au contact des produits chimiques et une impressionnante résistance à la fonte en cas d’exposition à une chaleur élevée ou au feu. En outre, le para-aramide est un tissu confortable qui permet aux produits de protection balistique d’être plus légers. Ces caractéristiques sont d’une grande importance pour la production de produits de protection balistique légère et/ou renforcée. En outre, les fibres para-aramides absorbent très bien les vibrations. Cela leur permet d’être utilisées dans les composants de protection qui seront exposés à de fortes vibrations et qui doivent présenter des propriétés d’amortissement.
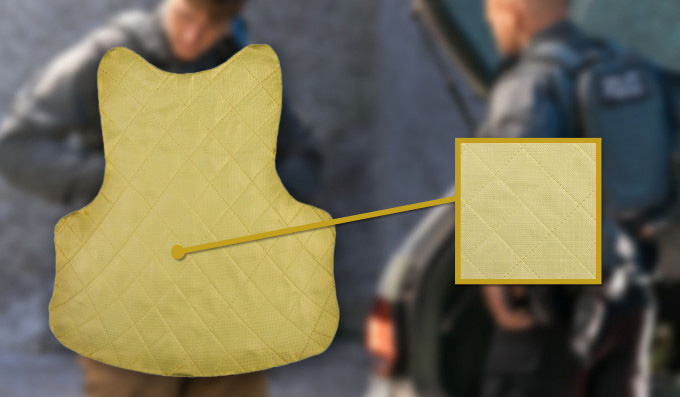
Qu’est-ce que le polyethylene haute performance ?
Le polyéthylène haute performance (HPPE) est un matériau synthétique considéré comme idéal pour la production d’équipements de protection balistique.
Le polyéthylène haute performance est principalement fabriqué par deux marques :
- Dyneema®
- Spectra®
Caractéristiques du polyéthylène haute performance
Les fibres en polyéthylène haute performance offrent une stabilité exceptionnelle par rapport à leur poids et présentent un faible allongement à la rupture. Le polyéthylène haute performance est très léger et résiste à tous les produits chimiques. Il résiste également à la lumière UV et aux autres éléments de la nature (c’est-à-dire aux intempéries).
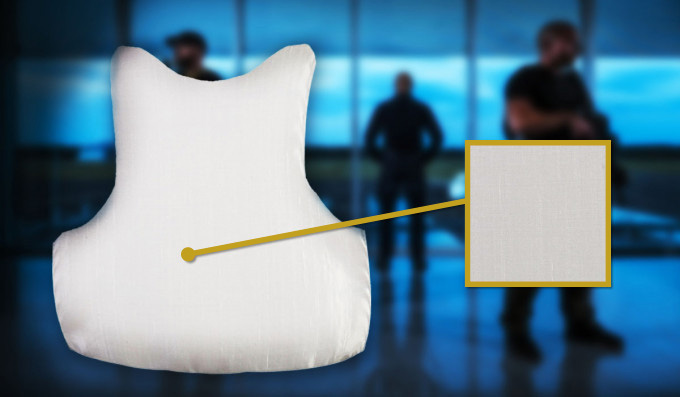
Difference entre le para-aramide et le polyethylene haute performanc
Il existe toutefois une différence importante : les fibres de polyéthylène haute performance sont presque toujours conçues en couches unidirectionnelles lorsqu’elles sont destinées à la balistique, tandis que les fibres para-aramides peuvent être utilisées soit en couches unidirectionnelles, soit sous forme de tissus.
Les couches unidirectionnelles commencent par une feuille de fil fortement parallélisée qui est liée à une deuxième feuille de fil alignée à un angle de 90 degrés par rapport à la première. La liaison est réalisée au moyen d’une matrice adhésive. Pour garantir des performances optimales, les couches unidirectionnelles sont généralement entourées d’un film protecteur extérieur.
Les avantages de chaque matériau doivent être évalués au cas par cas et en fonction des priorités fixées. Dans de nombreux cas, les différences de processus nécessaires à la fabrication des inserts de protection (tissu ou couches unidirectionnelles) comptent beaucoup plus que les différences de propriétés des fibres elles-mêmes.
Résistance et durabilité
Le HPPE présente le rapport résistance à la traction/masse le plus élevé de toutes les fibres disponibles. Il est 15 fois plus résistant que l’acier, avec une résistance à la traction d’environ 3,8 à 3,9 N/tex (en revanche, le para-aramide a une résistance à la traction de 2,03 à 2,06 N/tex). La composition moléculaire du HPPE rend le matériau beaucoup plus durable et résistant aux forces abrasives que les fibres para-aramides.
Le HPPE et le para-aramide sont tous deux utilisés depuis longtemps pour les gilets de protection — plus de 15 ans dans le cas du HPPE et plus de 30 ans pour le para-aramide.
En ce qui concerne les exigences des gilets de protection TR utilisés par la police allemande, la différence entre les couches unidirectionnelles et les tissus para-aramides peut être résumée comme suit : Les ensembles avec des couches unidirectionnelles ont tendance à être un peu plus légers que ceux des constructions de protection comparables utilisant des tissus para-aramides ; cependant, les constructions en tissu sont plus flexibles et donc mieux à même d’épouser les formes du corps des différents porteurs tout en permettant une bonne liberté de mouvement pour tous.
Performance multicoups
Les résultats des essais de traumatisme contondant et ce que l’on appelle la “performance multi-coups” tendent à être meilleurs pour les couches unidirectionnelles. Cela est dû à la plus grande rigidité des couches. Toutefois, les couches unidirectionnelles présentent l’inconvénient d’être relativement faciles à broyer et à plier, ce qui, dans les cas extrêmes, peut entraîner des plis et une délamination permanents.
Il est souvent avancé que le polyéthylène haute performance, en tant que matériau thermoplastique, est hautement inflammable et que cela représente un danger pour les policiers qui portent des produits de protection balistique fabriqués à partir de ce matériau.
En règle générale, toutefois, le potentiel d’un tel danger est minimisé parce que la protection balistique est enfermée dans le revêtement du gilet. En cas de port d’un gilet dissimulé, le panneau balistique est placé sous une couche de vêtements. Toutefois, si l’on souhaite une plus grande tranquillité d’esprit, le panneau balistique peut être placé à l’intérieur d’un revêtement extérieur ignifugé.
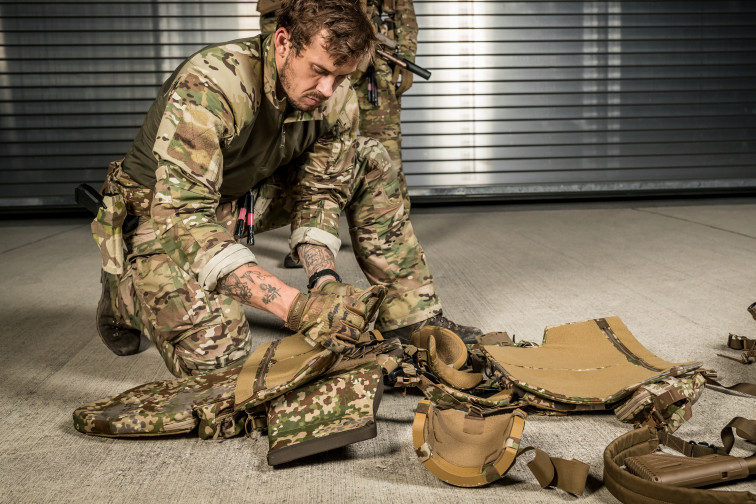
Potentiel de performance du polyéthylène haute performance
Le potentiel de performance du polyéthylène haute performance et du para-aramide doit être évalué en fonction des projectiles utilisés. Certains projectiles ont tendance à être arrêtés plus efficacement avec le para-aramide tandis que d’autres sont plus facilement arrêtés avec le polyéthylène haute performance.
Outre le para-aramide et le polyéthylène haute performance, une autre fibre très résistante, le PBO (nom de marque : Zylon®), a été utilisée pour les gilets de protection. Le PBO a connu son heure de gloire il y a quelques années, mais il a depuis presque complètement disparu du marché de la protection balistique.
Matériaux utilisés pour la production de balistiques légère
Les fibres textiles principalement utilisées pour la balistique légère sont le para-aramide et le polyéthylène haute performance. Ces matériaux sont soit tissés, soit intégrés dans des couches de fibres unidirectionnelles afin de fournir une protection efficace contre de nombreux types de balles tirées à partir de pistolets et de revolvers.
En outre, diverses formulations de plastiques sont utilisées pour créer des amortisseurs qui recouvrent certaines parties vitales du corps ou des sections entières.
Il est souvent possible de développer un panneau balistique spécifique pour la protection contre une menace potentielle particulière en utilisant une combinaison optimale des matériaux dont nous avons parlé.
L’âge dégrade les propriétés de tous les matériaux synthétiques que nous avons mentionnés et ils sont sensibles aux effets de l’exposition à l’humidité et aux rayons ultraviolets. C’est pourquoi les inserts balistiques légers des gilets de protection sont généralement emballés sous film plastique.
Matériaux utilisés pour la production de balistiques renforcées
En ce qui concerne la balistique renforcée, qui implique une protection contre les balles très dures et rapides (généralement celles tirées par des carabines), le matériau de protection doit être capable de “fracasser” efficacement les projectiles entrants. Pour ce faire, il faut utiliser des plaques très dures combinées à un matériau balistique léger et/ou renforcé.
Ces plaques sont généralement fabriquées en polyéthylène comprimé ou en céramique (oxyde d’aluminium, carbure de silicium et B4C, par exemple) et fournies avec un support approprié. Le choix du matériau dépend de la menace potentielle. D’un point de vue réaliste, les seules solutions viables pour ” fracasser ” des balles extrêmement dures et pénétrantes sont les plaques en céramique (qui sont elles-mêmes relativement dures).
Résumé
On peut affirmer que le para-aramide et le polyéthylène haute performance sont idéaux pour la production de gilets pare-balles. Les avantages de chaque matériau doivent être évalués au cas par cas, en fonction des priorités fixées.
Dans de nombreux cas, les différences requises dans le processus de fabrication des inserts de protection (tissu ou couches unidirectionnelles) sont un facteur plus décisif que la différence réelle dans les propriétés des fibres.
Pour en savoir plus sur notre gilet dissimulé.