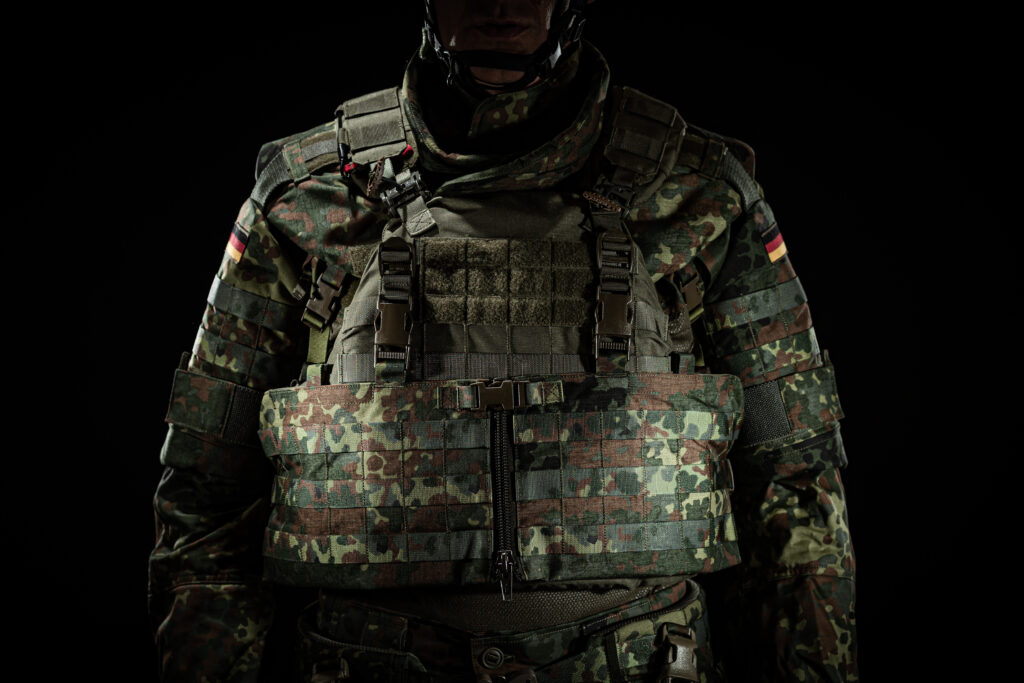
Aramid vs. polyethylene for use in bullet-resistant vests
It is nowadays hard to imagine police and military personnel routinely going about their lives without a bullet-resistant vest.
Bulletproof vests were first produced at the beginning of the 20th Century. At that time they were made of silk fibres. Silk was expensive and, owing to its cost, the material was deemed unsuitable for use in mass-produced protective vests.
In time a viable alternative was found in the form of aramid fiber fabric. Today, use of aramid has given way to para-aramid and polyethylene.
Para-aramid and polyethylene are extremely tensile synthetic fibers but are fundamentally different in their chemical compositions (they are visibly different too, judging by color alone: para-aramid is yellow, while polyethylene is white).
In this blog post:
- What is para-aramid?
- Characteristics of para-aramid
- What is high-performance polyethylene?
- Characteristics of high-performance polyethylene
- Difference between para-aramid and high-performance polyethylene
- Strength & durability
- Multi-hit performance
- Performance potential of high-performance polyethylene
- Which materials are used for the production of soft ballistics?
- Which materials are used for the production of hard ballistics?
- Summary
What is para-aramid?
Para-aramid is an industrially produced organic material made of aromatic polyamides (polyaramides). It was developed in the mid-1960s by US-based chemical company DuPont.
Today, para-aramid fibre is manufactured under various brand names, including:
- Kevlar®
- Twaron®
- Taparan®
- Technora®
Characteristics of para-aramid
Para-aramid fibres show high tensile strength at low stretching. This results in excellent ballistic protective characteristics against a wide range of bullet types. It also results in remarkable survivability from contact with chemicals and impressive melt-resistance against exposure to high heat or fire. Moreover, para-aramid is a comfortable fabric that also allows ballistic protection products to be lighter in weight. These characteristics are of great importance for the production of both hard-ballistic and soft-ballistic protection products. As well, para-aramid fibres are highly vibration-absorbent. This allows them to be utilized in protective components that will be exposed to strong vibrations and that need to exhibit damping properties.
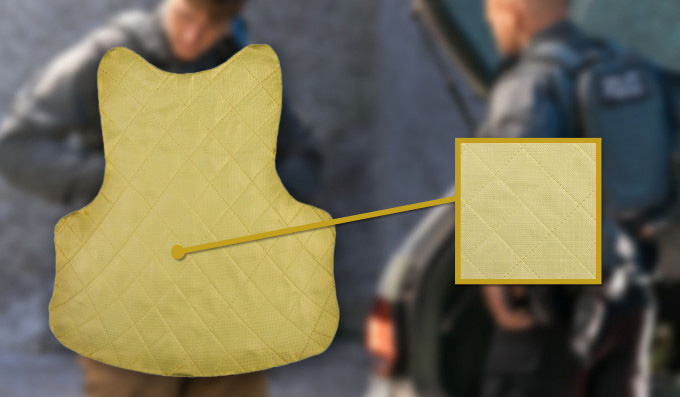
What is high-performance polyethylene?
High-performance polyethylene—HPPE in short—is a synthetic material considered ideal for the production of ballistic protection equipment.
High-performance polyethylene is manufactured mainly under two brand names:
- Dyneema®
- Spectra®
Characteristics of high-performance polyethylene
Fibres made of high-performance polyethylene offer exceptional stability in relation to their weight and have a low elongation at break. High-performance polyethylene is very light in weight and is resistant to all chemicals. It also stands up well to UV light and other elements of nature (ie, the weather).
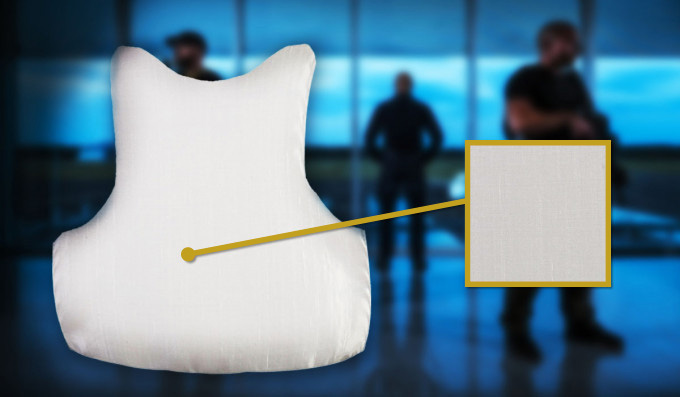
Difference between para-aramid and high-performance polyethylene
One significant difference, though: high-performance polyethylene fibres are almost always engineered in unidirectional layers if they are to be used for ballistics, while para-aramid fibres can be in either unidirectional layers or as woven fabrics.
Unidirectional layers begin with a strongly parallelized sheet of yarn that is bonded to the second sheet of yarn aligned at a 90-degree angle to the first. The bonding is achieved by means of an adhesive matrix. To ensure optimal performance, the unidirectional layers are usually enclosed within an outer protective film.
The advantages of each material must be evaluated on a case-by-case basis and in accordance with set priorities. In many instances, the process differences required to make the protective inserts (woven fabric or unidirectional layers) count for much more than the differences in properties of the fibres themselves.
Strength & durability
HPPE has the highest tensile strength-to-mass ratio of any fibre available. It is 15 times stronger than steel, with a tensile strength of about 3.8 to 3.9 N/tex (in contrast, para-aramid has a tensile strength of 2.03 to 2.06 N/tex). The molecular composition of HPPE makes the material much more durable and resistant to abrasive forces in comparison to para-aramid fibres.
Both HPPE and para-aramid have long been used for protective vests—over 15 years in the case of HPPE and more than 30 for para-aramid.
With reference to the requirements of the TR protective vests used by German police, the difference between unidirectional layers and para-aramid fabrics can be simply spelt out as follows: The packages with unidirectional layers tend to be a bit lighter than comparable protective constructions using para-aramid fabrics; however, the fabric constructions are more flexible and therefore better able to conform to the body shapes of different wearers while at the same time allowing good freedom of movement for all.
Multi-hit performance
Back-face signature (BFS) test results and so-called “multi-hit performance” tend to be better for unidirectional layers. This is due to the layers’ higher degree of stiffness. However, a disadvantage of unidirectional layers is they are relatively easy to crush and bend which, in extreme cases, can lead to permanent creasing and delamination.
It is often argued that high-performance polyethylene, being a thermoplastic material, is highly flammable and that this poses a danger to police officers who wear ballistic protective products made from the material.
As a rule, however, the potential for such a danger is minimized because the ballistic panel is encased within the vest cover. If a covert vest is worn, the ballistic panel is positioned under a layer of clothing. Still, if greater peace of mind is desired, the ballistic panel can be nested within a flame-retardant outer cover.
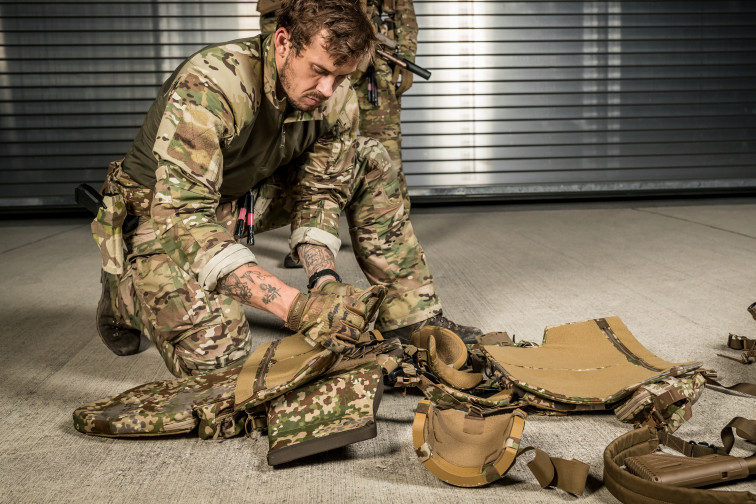
Performance potential of high-performance polyethylene
The performance potential of high-performance polyethylene and para-aramid must be assessed as a function of the projectiles used. Certain projectiles tend to be stopped more effectively with para-aramid while others are more easily halted with high-performance polyethylene.
In addition to para-aramid and high-performance polyethylene, another high-strength fibre PBO (brand name: Zylon®) was used for protective vests. PBO had its moment in the sun a few years ago but has since almost completely disappeared from the ballistic-protection market.
Which materials are used for the production of soft ballistics?
The textile fibres used predominantly for soft ballistics are para-aramid and high-performance polyethylene. These materials are either woven or else integrated into layers of unidirectional fibres to provide effective protection against many common types of bullets fired from pistols and revolvers.
Additionally, various formulations of plastics are used to create shock absorbers that cover certain vital parts of the body or entire sections.
Often it is possible to develop a specific ballistic panel for protection against one particular potential threat by using an optimal combination of the materials we’ve been discussing.
Age degrades the properties of all the synthetic materials we’ve mentioned, and they are sensitive to the effects of exposure to moisture and ultraviolet light. For these reasons, soft ballistic inserts for protective vests are customarily shrink-wrapped in plastic film.
Which materials are used for the production of hard ballistics?
With regard to hard ballistics—which involves protection against very hard and fast bullets (typically those fired from rifles)—the protective material must be capable of effectively “smashing” the incoming projectiles. This requires the use of very hard insert plates combined with soft ballistic material.
These plates are for the most part made of compressed polyethylene, or ceramics (e.g. aluminium oxide, silicon carbide, and B4C) and supplied with a suitable backing. The choice of material depends on the potential threat. Realistically, the only viable solutions for “smashing” extremely hard and penetrative bullets are ceramic plates (which themselves are relatively hard).
Summary
A strong argument can be made that para-aramid and high-performance polyethylene are ideal for the production of bullet-resistant vests. The advantages of each material must be weighed on a case-by-case basis in accordance with the priorities that have been set.
In many cases, the differences required in the manufacturing process for the protective inserts (woven fabric or unidirectional layers) are a more decisive factor than the actual difference in the fibre properties.
Learn more about our covert vest.