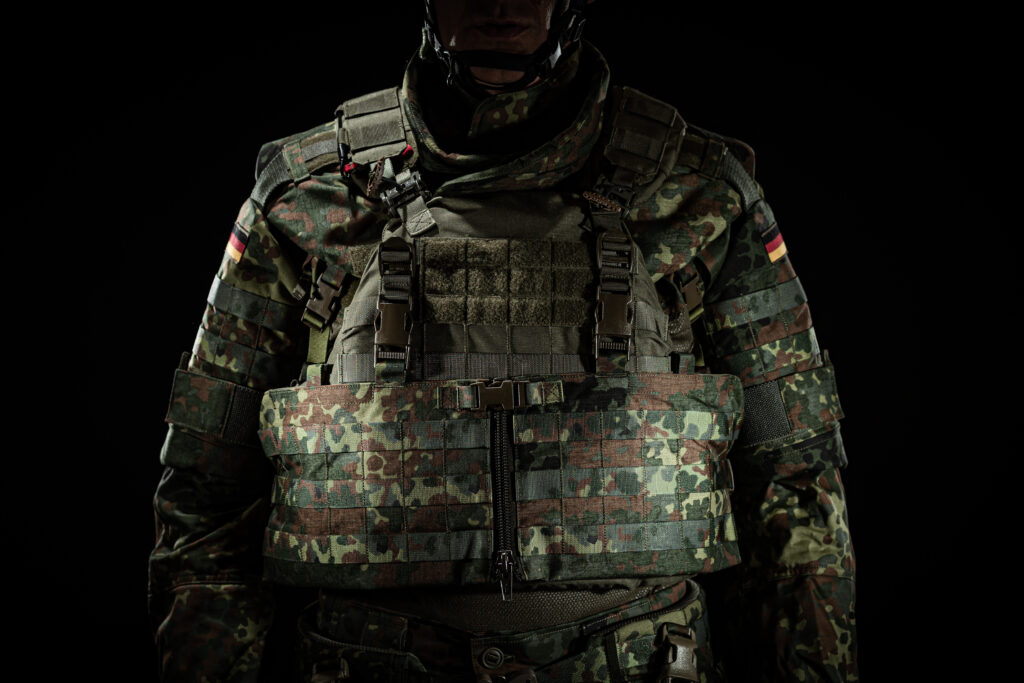
DIN 2303 – Requirements for the welding of armour steel
The quality of welding processes is paramount, particularly in safety-critical areas such as defence technology.
Since the quality of weld seams cannot be improved retrospectively, it must be guaranteed during the production process, necessitating strict standards. Additionally, the quality of a welded product cannot be sufficiently determined non-destructively during the process. DIN 2303 outlines the requirements for manufacturing and repair companies engaged in welding work on defence technology products.
In this blog post, we explore the key requirements of DIN 2303 and their significance for welding armour steel.
Classification of manufacturer qualification according to DIN 2303
DIN 2303 classifies companies into four manufacturer qualification classes based on material and safety requirements. These classifications depend on the type of product, the materials used, and any specific additional requirements. Each classification comes with corresponding quality standards that must be met.
Class Q1 includes general requirements and applies to companies that work with standardised materials without increased requirements for processing the material. This category encompasses unalloyed structural steels, simple austenitic stainless steels, and non-hardenable aluminum alloys.
Class Q2 involves special requirements and applies to companies that work with special materials, such as liquid-tempered steels or heat-treatable aluminium. Due to the increased requirements of these materials, additional processing regulations, such as Construction Regulation (BV) 1050 for naval shipbuilding, may need to be adhered to.
Class Q3 applies to companies that process armouring materials that must comply with the specifications of the Bundeswehr Technical Delivery Conditions.
Specifically, this includes TL 2350-0003 for armour steel and TL 2350-0008 for armour aluminum.
Note: This TL covers not only welding but also other manufacturing processes (special processes) such as cold forming or thermal flame cutting.
Class Q4 is intended for companies that manufacture components from special materials for aviation. As these components must meet the highest safety and quality standards, compliance with specific aviation regulations is required.
Q3 welding represents the highest requirement for processing armour materials and is essential for armoured vehicles, military protective structures and critical infrastructure projects.
Component classification and quality requirements
Quality assurance plays a key role in defence technology products. The quality requirements depend on the class of the component. DIN 2303 classifies defence components into four classes according to their function and type of stress.
The requirements for load-bearing capacity, safety and usability vary depending on the component class.
Simplified description of the component classes:
- Component class 1: This class includes defence technology products with high stresses and high safety significance, etc. It requires the most stringent quality control and material requirements.
- Component class 2: Products in this class are subject to normal stresses and have a medium safety significance, etc. The requirements are moderate, but still relevant to safety.
- Component class 3: These are components with low stress and low safety significance, etc. Quality requirements are reduced accordingly.
- Component class 4: This class is determined on a case-by-case basis, depending on specific product requirements and areas of application.
Component class | Description |
BK1 | This class applies to the manufacture of defence technology products or their individual components with high static or dynamic loads and high safety significance and/or high operational capability. |
BK2 | This class applies to the manufacture of defence technology products or their individual components with normal static or dynamic loads and medium safety significance and/or medium operational capability. |
BK3 | This class applies to the manufacture of defence technology products or their individual components with low static or dynamic stress and low safety significance and/or low operational capability. |
BK4 | This class applies to the manufacture of defence technology products or their individual components with low static or dynamic stress and low safety significance and/or low operational capability. |
It is important to note that the required quality of components and assemblies is derived from the component classes. This means that highly stressed assemblies require high component quality!
Additionally, the requirements for qualified welding supervisors are also derived from the component classes. For instance, high component class 1 components require a welding engineer (SFI) in accordance with DVS-IIW/EWF 1173 for welding supervision to ensure professional processing and quality assurance.
Defence technology products with armouring function
The manufacturer qualification of class Q3, in accordance with DIN 2303 is specifically intended for companies that manufacture components with armouring functions. These products must meet the highest safety standards, as they are exposed to unique threats in the military sector, including ballistic threats and explosives.
Qualification for this class requires compliance with specific regulations, in particular the technical delivery conditions (TL 2350-0003 and TL 2350-0008). TL 2350-0003 outlines the specifications for the design, manufacture and testing (approval) of enclosures with armouring functions. This regulation specifies detailed technical requirements to ensure that the manufactured components provide the required protection in use.
A special process test, which verifies the welding process, includes the production of three basic blast bodies. These must be manufactured by the company in accordance with the requirements of TL 2350-0003. The test pieces are then tested by the Weapons and Ammunition Technical Centre (WTD 91) to assess the weld seam quality. Only after successful testing can the company obtain approval to manufacture armour components.
Proven basic blast body for preliminary tests
Components with an armouring function are generally assigned to the highest component class 1. This means that they are subject to high stresses and are of the utmost importance in terms of safety. The quality requirements and the necessary testing and approval procedures for manufacturers in this class are correspondingly strict.
Recognised bodies
The “recognised bodies” play a central role in the approval process for manufacturers in accordance with DIN 2303. Their primary task is to ensure that companies meet the necessary quality and process requirements before receiving manufacturer approval.
The recognised bodies take on the following tasks, among others:
- Checking the application: The company’s application is first reviewed to ensure that all required documents have been submitted completely and correctly.
- Company audit and inspection: An on-site audit follows, during which the company’s premises, production processes, and quality assurance measures are evaluated.
- Technical discussion with the welding supervisor: A technical discussion with the responsible welding supervisors is another important requirement, aimed at assessing their expertise and competence.
- Issue of the manufacturer’s licence: After successful meeting all criteria, the recognised body issues the manufacturer’s licence in accordance with DIN 2303.
- Forwarding the results to the civilian control centre
Summary
Welding according to DIN 2303 is a requirement of the German Armed Forces and is categorised into quality requirements and component classes.
The quality requirements are divided into four manufacturer qualifications (Q1 to Q4), each corresponding to specific defence technology products and materials. Component classes determine the required quality standards for parts and assemblies.
For armour steel welding, DIN 2303 mandates manufacturer qualification Q3, with additional requirements specified in TL 2350-0003.
Mehler Protection obtained initial approval for manufacturer qualification Q1 in accordance with DIN 2303 in October 2021. In October 2023, the approval was extended to include class Q2. Approval for the processing of armour steel sheet (Q3) was obtained in December 2024. An extension to other processes and materials (e.g. armour aluminium or additive manufacturing processes) is planned.
Sources
- DIN 2303 – Welding and allied processes – Quality requirements for the manufacture and repair of defence-related products – Status February 2007.
- TL 2350-0003 – Armoured enclosures – Design, manufacture and testing – Version 27.03.2014
Images and graphics: Mehler Protection, Mehler Engineered Defence GmbH (All rights reserved, 2025)