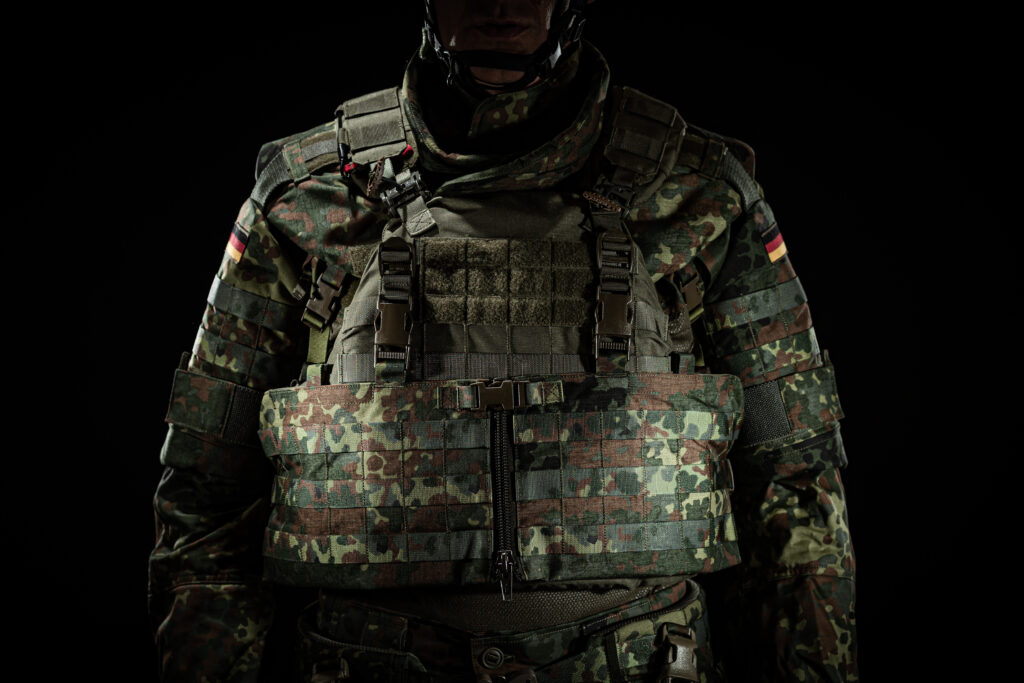
EASA approval of ballistic protection components
Ballistic add-on armour plays a crucial role in the safety of equipped aircraft, particularly in military and security contexts. However, integrating protection systems of this kind requires meticulous planning and certification to ensure airworthiness and compliance with European safety standards.
In this blog, we explore the specifics of EASA approval for ballistic add-on armour and the associated challenges, while also providing an overview of the certification process.
In this blog post:
General information on EASA approval
The European Union Aviation Safety Agency (EASA) is the central European authority for civil aviation and is responsible for the certification of aircraft and their components within the European Union. The certification process ensures that all aircraft comply with the defined safety and environmental standards. The approval process itself must be initiated and carried out by an EASA-certified design organisation.
This process consists of four main phases:
- Technical familiarisation and certification basis: The aircraft design or proposed modification is presented and the relevant safety and environmental protection requirements are defined in consultation with EASA.
- Establishment of the certification program: The applicant proposes a program describing the methods for achieving compliance with the requirements.
- Compliance demonstration: Compliance with the requirements is demonstrated through analyses, simulations and tests.
- Technical closure and issue of approval: Once compliance with all requirements has been successfully demonstrated, EASA issues the certificate.
This structured approach ensures full and due regard for all aspects of airworthiness and safety.
Specifics of add-on armour with EASA approval
The integration of ballistic protection systems in aircraft presents specific challenges:
- Weight and centre of gravity: Ballistic protective materials increase the total weight of the aircraft and affect its centre of gravity. Careful analysis and adaptation are necessary to ensure flight stability.
- Structural integrity: Add-on armour must be installed in such a way as to meet the flight load requirements and achieve the necessary safety factors. In addition, it must be demonstrated that there is no impairment of the aircraft’s structural integrity. This calls for extensive analyses and tests, and – where necessary – modifications or reinforcements of the existing structure.
- Aerodynamics: Add-on armour can increase drag and change aerodynamic properties, thereby affecting the performance and efficiency of the aircraft.
- System integration: The new protection systems must be integrated seamlessly into the aircraft’s existing systems, including the electrical, avionics and emergency systems. In addition, it must be ensured that any potential modifications do not unduly increase or negatively affect the workload of the pilot(s).
Image: Integrated system solution
These factors require close cooperation between developers, designers, engineers and certification authorities to ensure that add-on armour meets the high standards of the aviation industry.
Challenges of the certification process
Certifying ballistic add-on armour for aircraft is a complex process that involves several challenges:
- Demonstration of ballistic performance: Extensive testing must be carried out to ensure that the protection systems can withstand the required threat levels.
- Documentation: All design, test and integration processes must be comprehensively documented to demonstrate compliance with EASA regulations.
- Time and cost: The certification process can be time-consuming and costly, especially if unexpected problems arise necessitating additional testing or design changes.
- Continuous monitoring: After certification, the protection systems must be regularly inspected and maintained to ensure their effectiveness and conformity.
These challenges underline how crucial early planning and close cooperation with EASA and other relevant bodies are to the success of the certification process.
Approval of materials used for ballistic add-on armour
A key aspect of obtaining EASA approval for ballistic add-on armour is the approval of the materials used. These are subject to stringent requirements and testing procedures because they have such a major impact on the protective effect, weight and structural integrity of the aircraft.
Material requirements:
- Ballistic performance: The materials must demonstrate that they can withstand the specified threat levels without losing their structural integrity. For this purpose, standardised ballistic tests are carried out to check resistance to different types of ammunition and impact angles.
- Weight and strength: In aviation, weight is a critical factor. Therefore, the materials must not only be resistant, but also lightweight to avoid adversely affecting flight performance. Frequently used materials are:
- Aramid or polyethylene fibres – low weight, high tensile strength.
- Ceramic composites – high levels of hardness and resistance to armour-piercing ammunition.
- Fire protection and smoke generation: To ensure the safety of occupants, EASA requires proof that the materials used do not emit toxic vapours in the event of fire and that they are flame-retardant.
- Environmental resilience: The materials must be able to withstand extreme temperature ranges, humidity and other environmental conditions without losing their protective effect.
Testing and approval procedures:
Material testing and certification: Before a material is approved for use, it undergoes a series of tests, including:
- Structural tests: It is necessary to verify mechanical properties such as tensile strength and bending strength.
- Fire and smoke tests: EASA conformity must be ensured with regard to fire resistance and smoke generation.
All test reports and material properties must be documented in detail and submitted to EASA for review. This documentation must also include the origin of the materials and details of the associated production processes to ensure consistency and quality. After approval, the materials must undergo continuous quality control to ensure that each batch meets the defined specifications.
Requirements for design and special properties
EASA approval of ballistic add-on armour encompasses far more than just the testing of the materials and the performance. Rather, the aspects discussed below apply to all phases of design, integration, operation and maintenance. In particular, interactions with existing systems and compliance with strict safety and EMC standards make the certification process both demanding and time-consuming.
Electromagnetic compatibility (EMC)
Ballistic add-on armour can influence electromagnetic fields due to the materials used and how they are arranged. To ensure that there is no interference with the avionics and electronic systems, the following must be checked:
- EMC tests: It must be ensured that the add-on armour does not cause electromagnetic interference – and is not affected by it.
- Shielding effects and reflections: Testing is required to determine whether metallic or conductive materials cause unwanted reflections or interference in communication and navigation systems.
Emergency and evacuation plans
Ballistic add-on armour must not impair the safety of occupants, particularly in an emergency. Therefore, the following aspects must be considered:
- Emergency exits and accessibility: The protective systems must not block emergency exits or interfere with their proper functioning.
- Crash safety: In the event of an accident, no additional hazards must be created by splinters, fragments or detached protective parts.
Maintenance and servicing
Regular maintenance and inspection are required to ensure the long-term safety and effectiveness of the add-on armour. This involves compliance with the following:
- Maintenance concept: Preparation of a detailed maintenance plan specifying inspection intervals, test criteria and material replacement cycles.
- Repair procedure: Guidelines for professional repair or replacement of damaged protective components.
Note: Maintenance and repair must be carried out by an approved maintenance organisation according to EASA Part 145.
- Training of maintenance personnel: It must be ensured that maintenance personnel are trained and certified to meet the specific requirements of ballistic add-on armour.
Flight performance and operating limits
Ballistic protection systems can affect flight performance and operating characteristics, meaning that the following aspects must be checked and documented:
- Change in performance data: Manuals must be adjusted and effects on flight range, climb performance and manoeuvrability must be documented.
- Operating limits and payload: It is necessary to check whether the operating limits are affected by the shift in weight and centre of gravity.
Human factors and ergonomics
Add-on armour must be integrated in a way that avoids impairing operability and ergonomics for the flight crew and occupants:
- Field of vision and instrument accessibility: The view must not be obstructed and the operation of control instruments must not become more difficult.
Environmental and material compatibility
As aircraft are exposed to extreme environmental conditions, add-on armour must meet additional requirements when integrated externally:
- Corrosion resistance: Materials must not corrode in high-humidity or salty environments (e.g. naval aircraft).
- UV and temperature resistance: It is necessary to ensure material stability under exposure to high UV radiation and extreme temperature differences.
Chemical resistance: Materials must be protected against aggressive chemicals, such as hydraulic fluids, fuel or de-icing agents.
System integration and safety analysis
EASA approval for ballistic add-on armour in aircraft requires precise system integration and a comprehensive safety analysis according to the relevant regulations (e.g. CS-27/CS-29 for helicopters, CS-23 for aeroplanes).
01. Functional Hazard Assessment (FHA):
- Identification of potential hazards and their impact on aviation safety.
- Classification of hazard levels (e.g. Minor, Major, Hazardous, Catastrophic)
02. System requirements definition:
- Determination of safety-critical requirements based on the results of the FHA.
- Definition of functionalities and safety objectives for the add-on armour.
03. Preliminary System Safety Assessment (PSSA):
- Analysis of system architecture and identification of safety requirements.
- Preliminary risk assessment and definition of safety measures.
04. Detailed design & implementation:
- Development and design of add-on armour according to the defined requirements.
- Integration into the aircraft while taking into account the safety objectives.
05. System Safety Assessment (SSA):
- Review and validation of the entire system after implementation.
- Tests and security analyses to verify requirements.
06. Certification & approval:
Submission of documentation and evidence to EASA.
- Official testing and issuing of approval for use of the add-on armour.
Security analysis process: FHA and SSA
Production and assembly
Approving a change is only one part of the task. After approval, the design organisation possesses a set of approved production documents or design data.
Based on this design data, the relevant components/assemblies can be manufactured by a production organisation that has been approved by EASA or by the competent national aviation authority (in this case: the German Federal Aviation Office). A corresponding agreement (DO-PO Agreement) is concluded between the design organisation and the production organisation, governing how the production documents are to be handled and any potential deviations.
The production organisation itself then prepares its own production instructions based on the approved design data from the design organisation. These production instructions (drawings, step-by-step instructions, protocols) serve as the foundation for producing the armour at the production organisation.
Approving a change is only one part of the task. After approval, the design organisation possesses a set of approved production documents or design data.
Based on this design data, the relevant components/assemblies can be manufactured by a production organisation that has been approved by EASA or by the competent national aviation authority (in this case: the German Federal Aviation Office). A corresponding agreement (DO-PO Agreement) is concluded between the design organisation and the production organisation, governing how the production documents are to be handled and any potential deviations.
The production organisation itself then prepares its own production instructions based on the approved design data from the design organisation. These production instructions (drawings, step-by-step instructions, protocols) serve as the foundation for producing the armour at the production organisation.
Approved example products:
At the end of the production process, the manufactured articles are checked and released internally by the authorised personnel (certifying staff).
The certifying staff release and confirm airworthiness using EASA Form 1.
Unless an EASA Form 1 has been issued, the end customer or responsible maintenance organisation is not authorised to install the relevant item in the aircraft. In the case of initial fitment, the form applies to the complete assembly and the corresponding installation kits. For any subsequent replacements that the customer wishes or is required to carry out, a corresponding release certificate is likewise required.
A further airworthiness certificate is also required if, for example, a protective plate comes in for repair. In this case, the release must be issued by an approved maintenance organisation, which carries out this repair on the basis of approved maintenance and/or repair instructions.
Summary
Integrating ballistic add-on armour into aircraft poses complex technical and regulatory challenges. As well as requiring structural adaptation to the existing airframe, it also involves taking into account factors such as weight, aerodynamics, energy absorption and interaction with other aircraft systems.
The comprehensive safety analysis plays a crucial role in approval by the European Union Aviation Safety Agency (EASA). This is carried out according to recognised methods – such as the System Safety Assessment (SSA) as per ARP 4761 – and includes, amongst other things, a Failure Modes and Effects Analysis (FMEA), as well as an evaluation of structural integrity and electromagnetic compatibility.
In addition, the protective systems must be tested according to relevant ballistic standards (e.g. STANAG 4569, NIJ 0108.01 or VPAM) to ensure that the required protective effect is achieved without adversely affecting operational safety or flight characteristics. EASA compliance is demonstrated through design reviews, test documentation and close coordination with the regulatory authority to obtain either a Supplemental Type Certificate (STC) or a Minor Change Approval.
The final production of the components is also subject to regulation and release by the aviation authority. Production, assembly and maintenance may only be carried out by an approved organisation.
Images and graphics: Mehler Protection, Mehler Engineered Defence GmbH (All rights reserved, 2025)