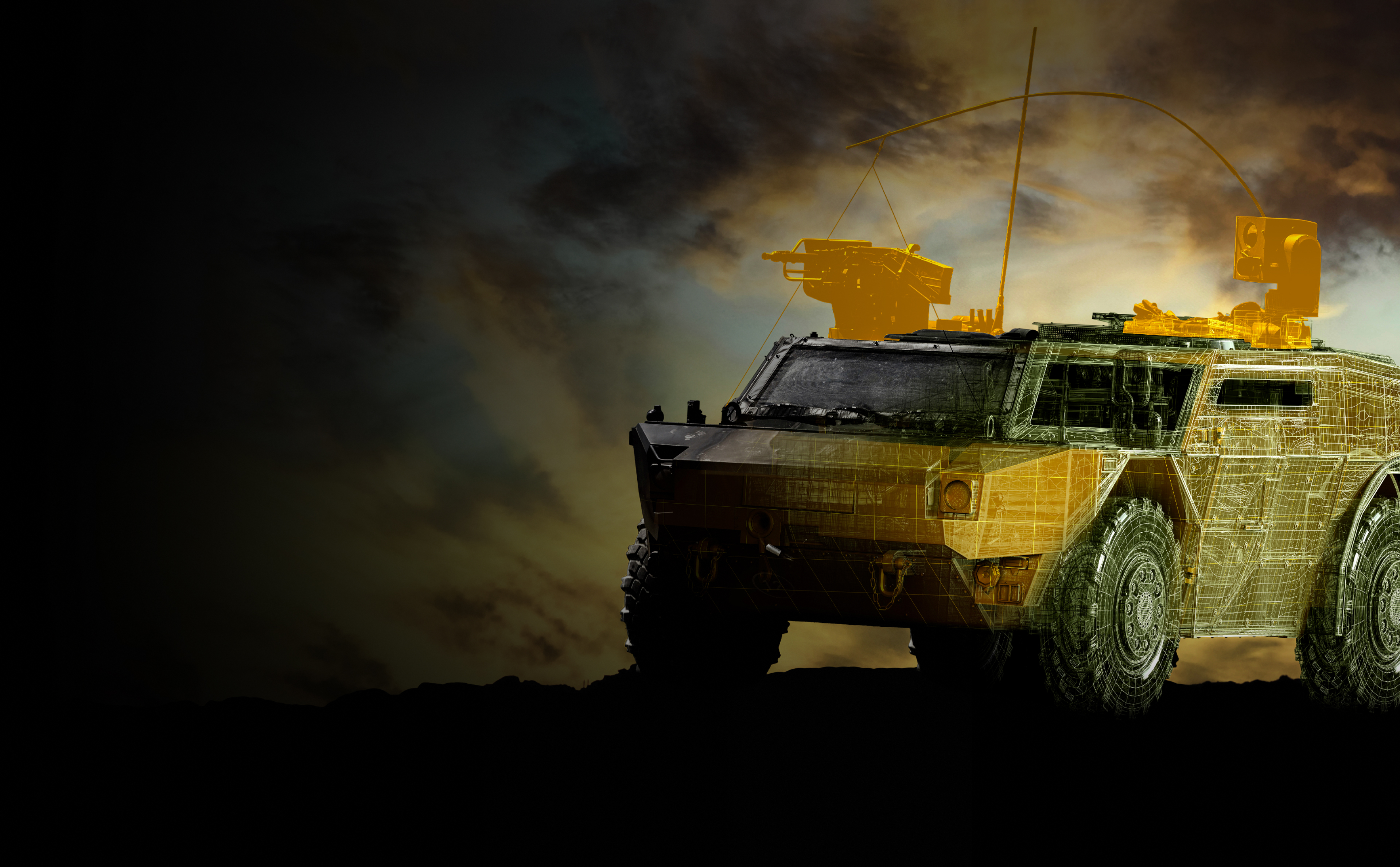
Protec3d
Send Inquiry
Thank you!
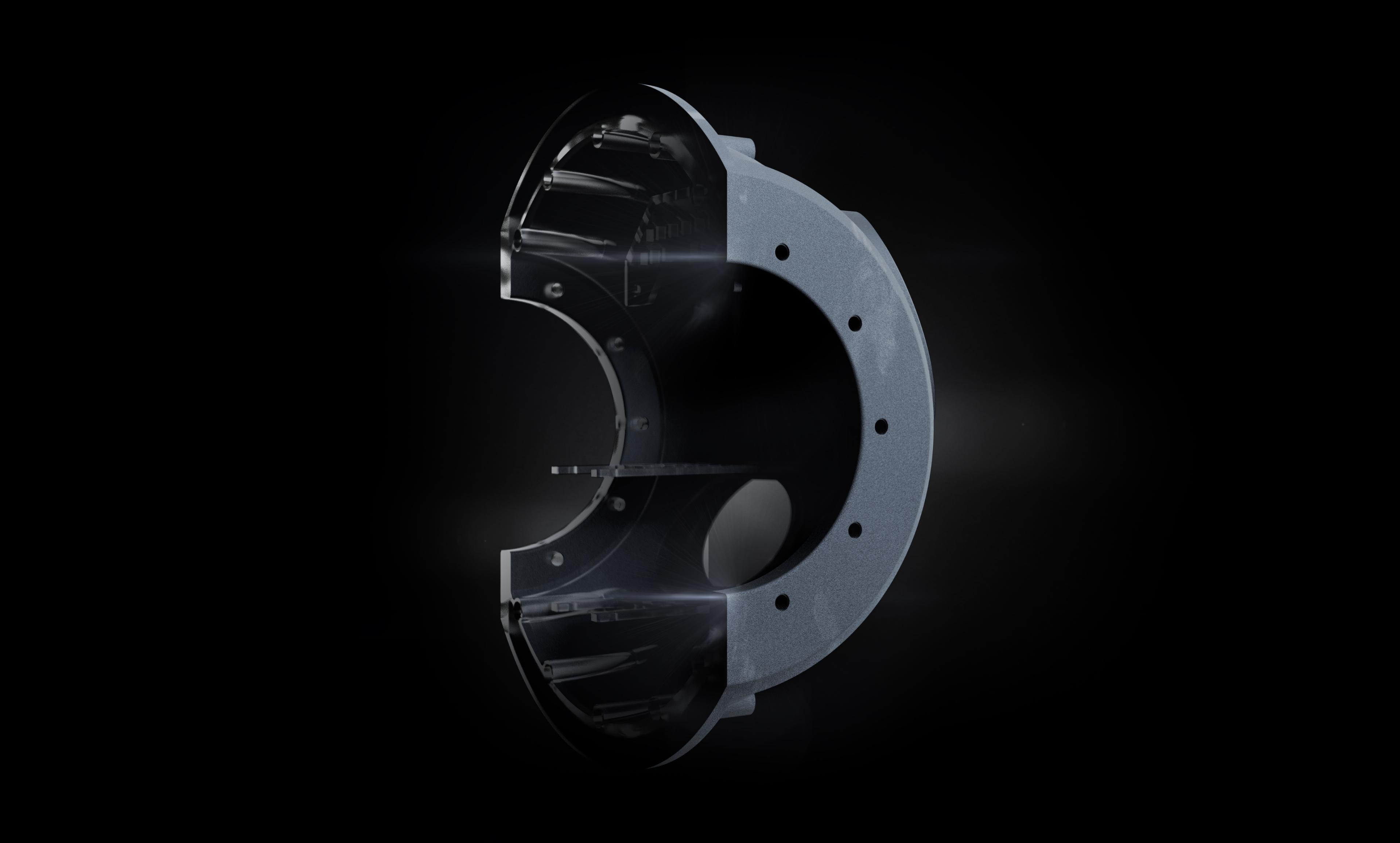
Freedom of Design
A crucial advantage of PROTEC3D is the virtually unlimited design freedom. 3D printing allows for the creation of complex structures and shapes to enable the development of custom-made protection solutions that are perfectly tailored to specific requirements and operational conditions.
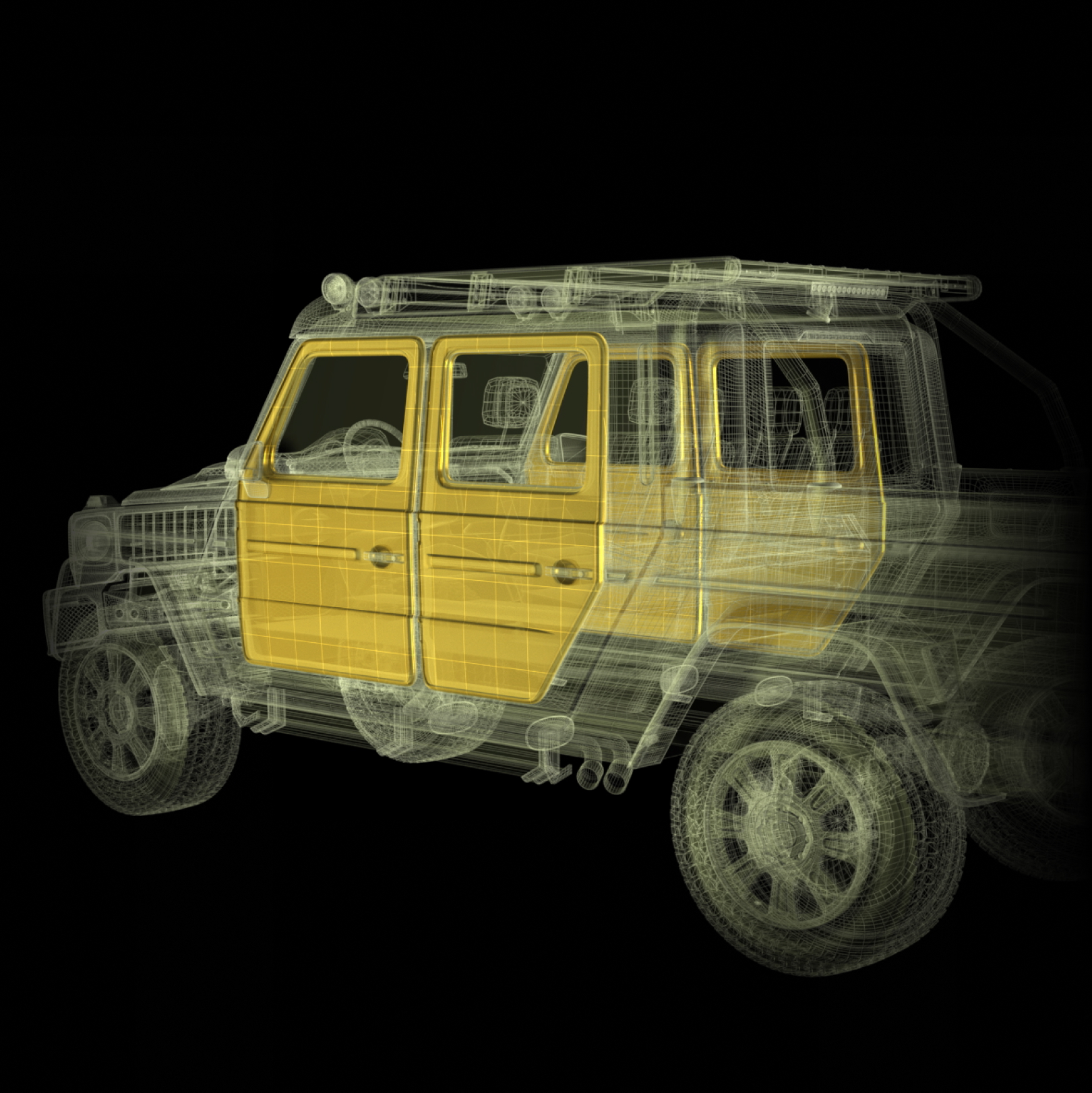
REAL-WORLD ADAPTION
PROTEC3D is already successfully used in civil protection vehicles. For example, window frames with VPAM 9 protection levels have been created with significant weight savings. Ongoing development and application-based adaptation promise to transform ballistic protection solutions and open up innovative approaches for the future.
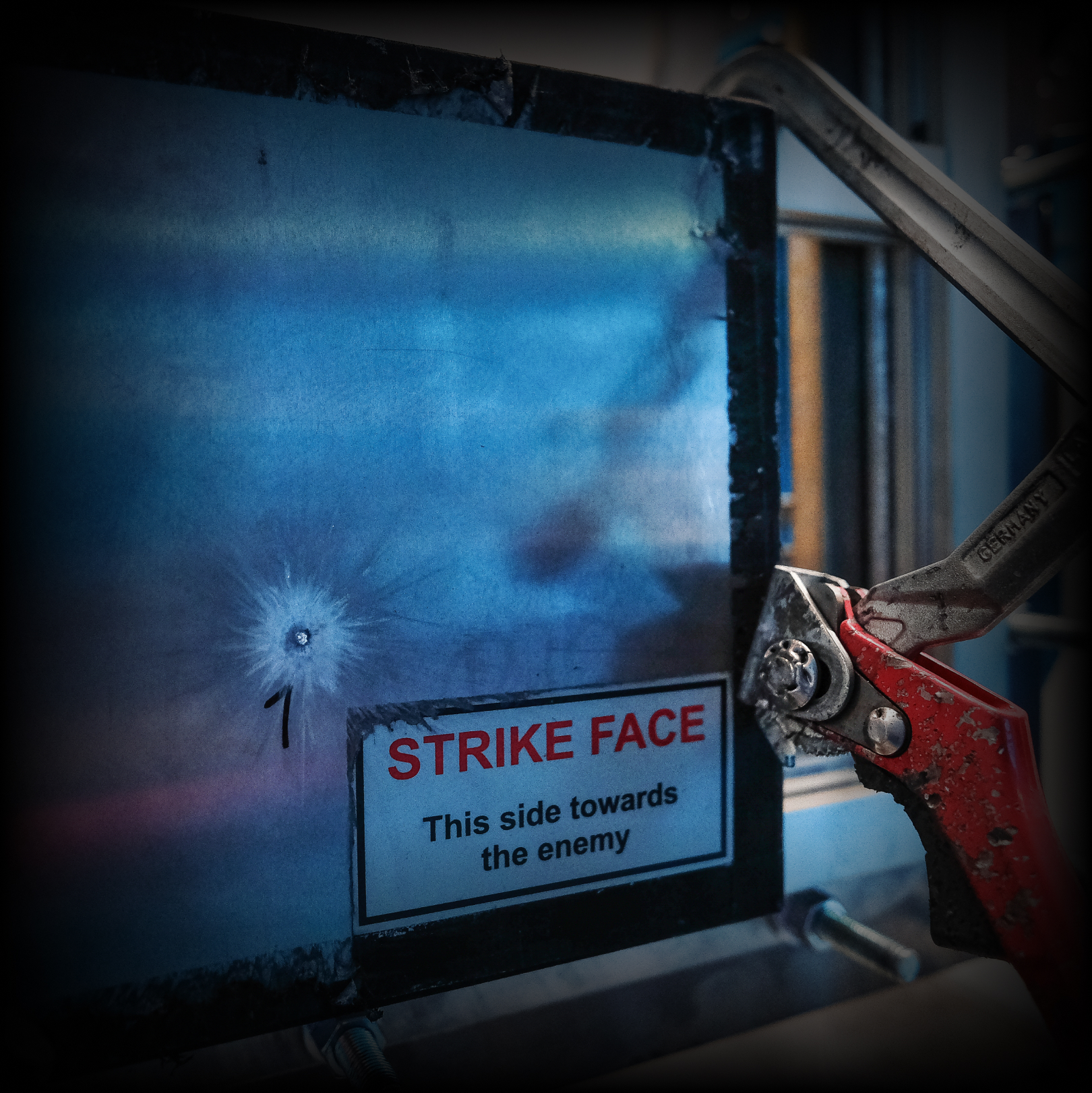
Superior ballistic protection
Ballistic performance is a critical factor in protection solutions and this is where PROTEC3D excels. Its layer-by-layer manufacturing process allows precise control of material properties, ensuring consistent resistance to ballistic threats. In addition, mechanical properties can be further optimised through targeted adjustments in printing technology and post-processing.
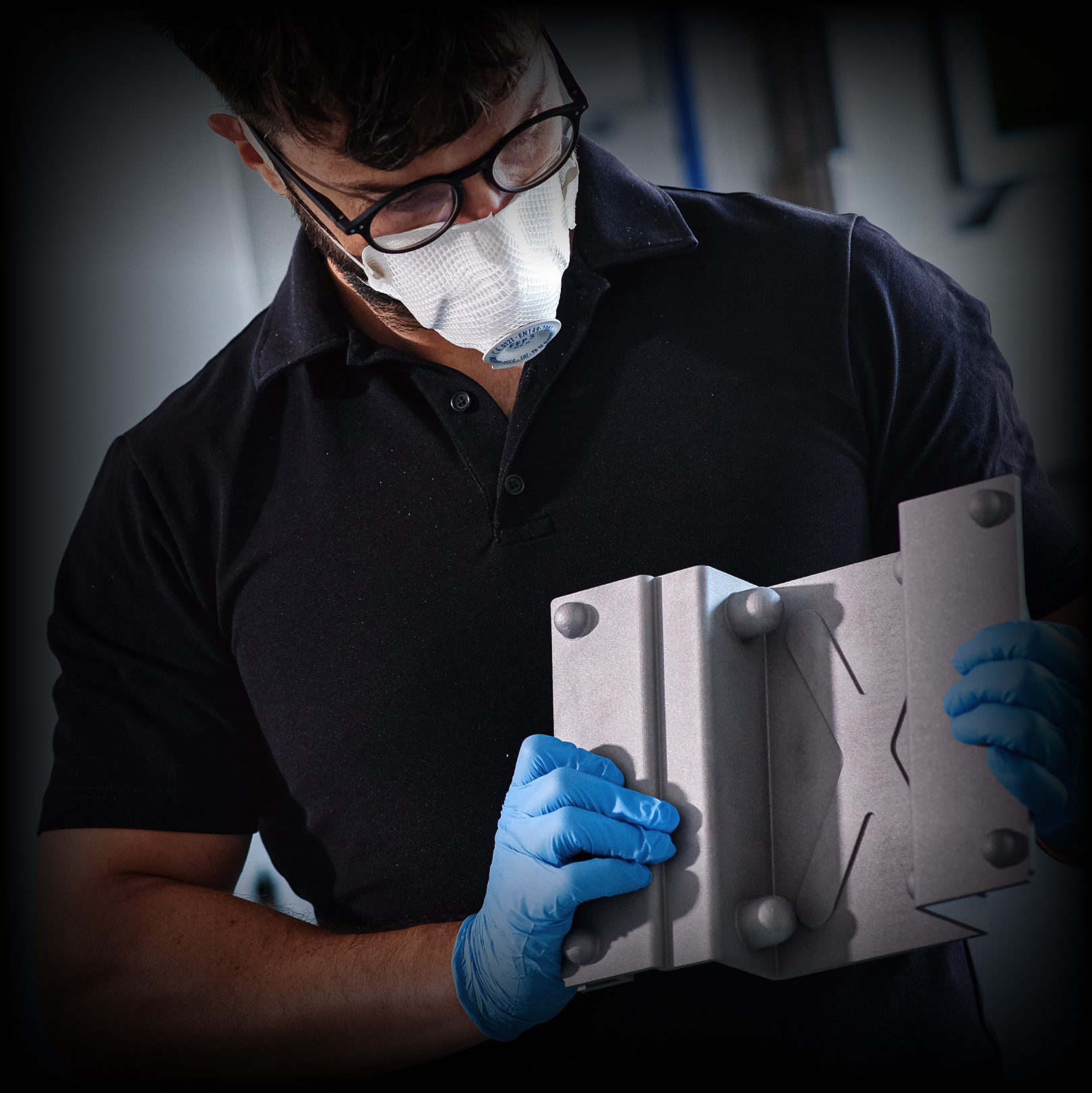
SHORT LEAD TIMES AND COST EFFICIENCY
A major advantage of PROTEC3D is the significant reduction in lead times and associated cost efficiency. Additive manufacturing optimises material usage by processing only what’s needed, reducing waste and costs. These benefits enable faster, more flexible and cost-effective ballistic protection solutions, which is particularly valuable in time-critical, resource-intensive scenarios.
FUNCTIONAL INTEGRATION
PROTEC3D enables the integration of additional functions directly into the component, reducing the need for subsequent assembly steps and increasing the reliability and lifespan of protection solutions. This integration also enhances operability and maintainability by providing a more comprehensive, multifunctional protection solution.
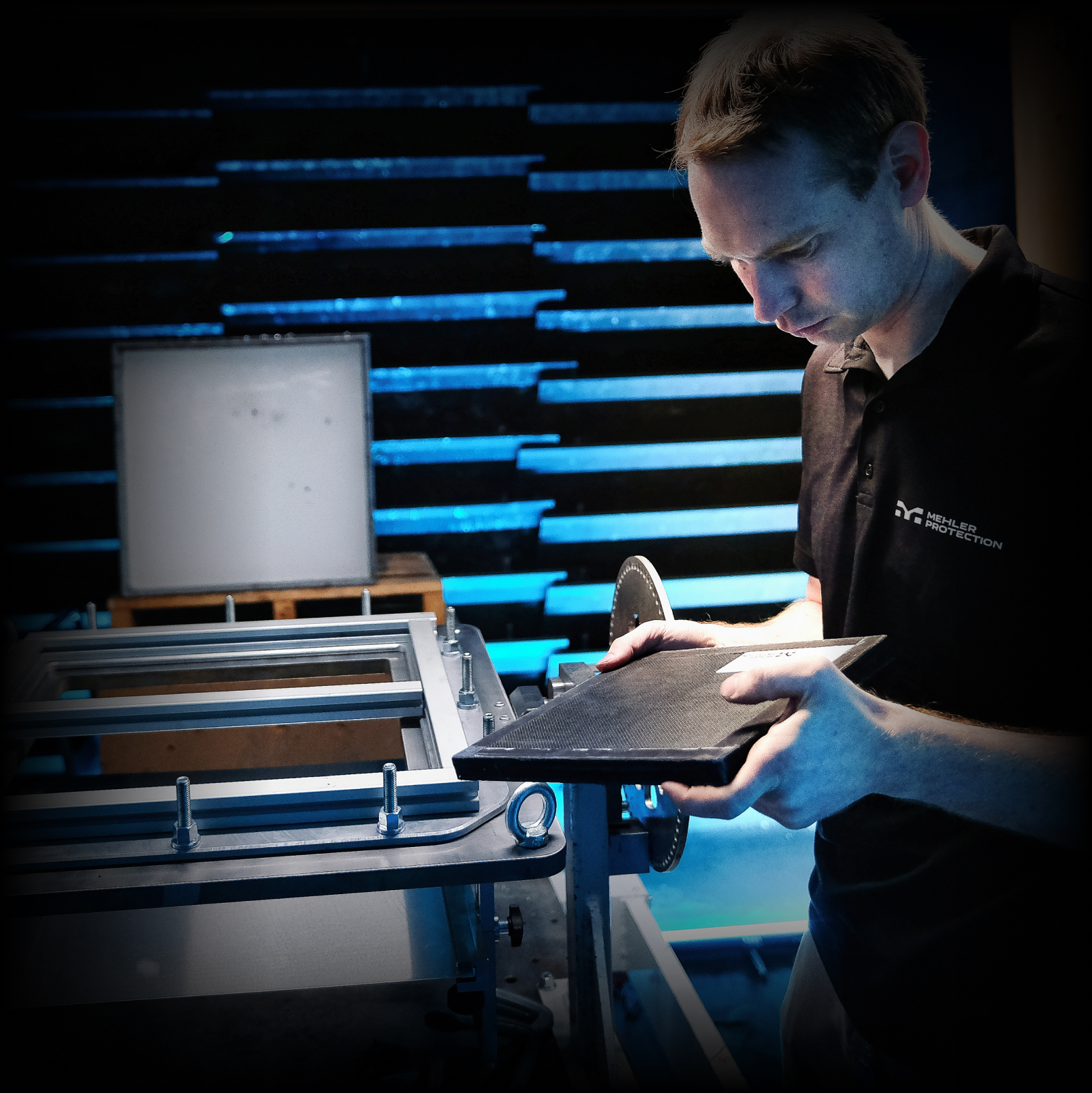
WEIGHT OPTIMIZATION
A key advantage of PROTEC3D is its ability to achieve application-specific design optimisation, resulting in significant weight reduction. Additive manufacturing places material only where it is needed for ballistic protection and structural integrity.
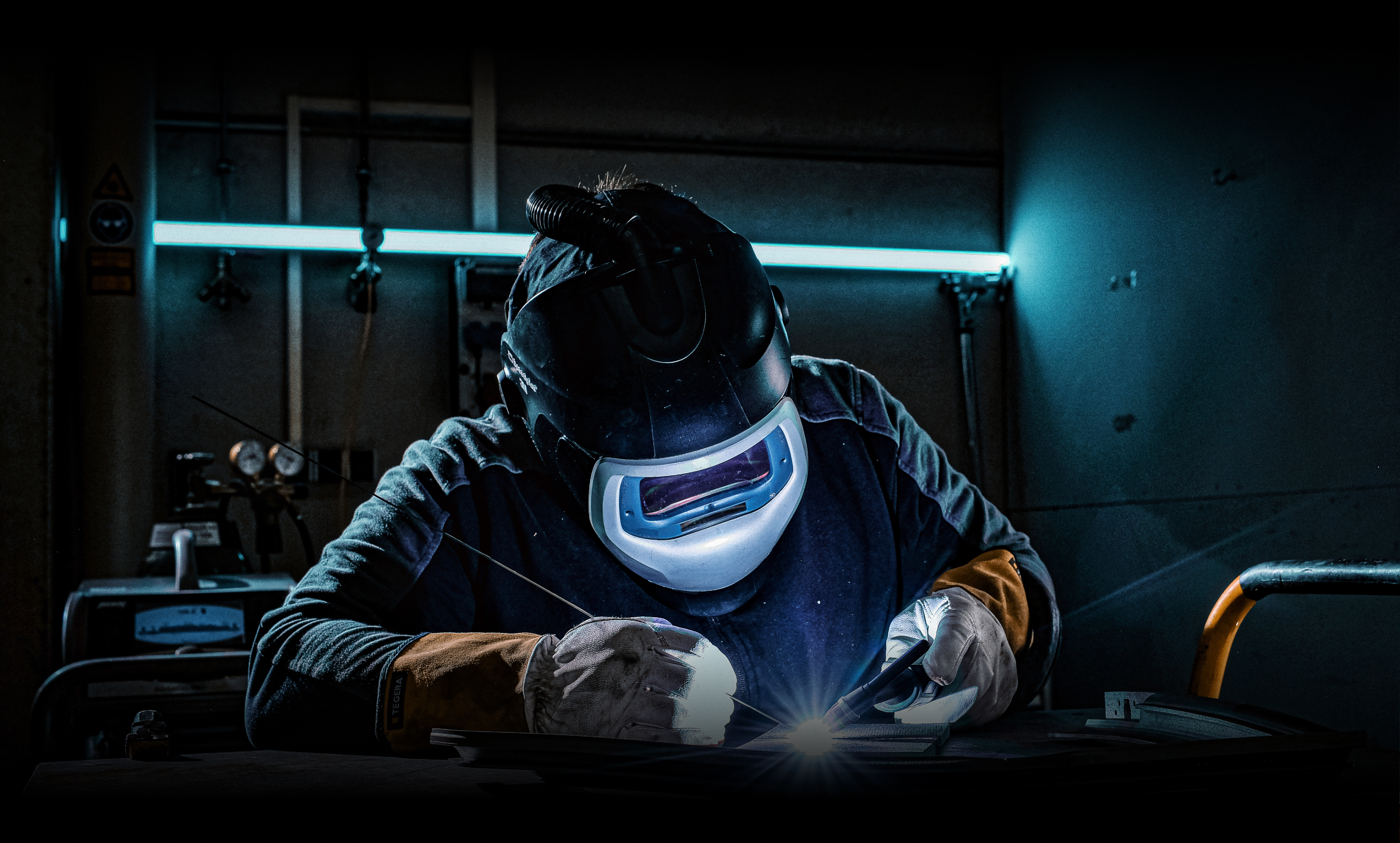
Realisation of large components
A Selective Laser Melting (SLM) process is used to produce components through 3D printing. By welding these 3D-printed components with the same alloy, even very large parts can be realized. A subsequent heat treatment process achieves hardness levels of 400-620HB, resulting in a homogeneous component without weak points at weld seams, heat-affected zones, or hardness variations.